Transforming Pharma: Digital, Collaborative, Data-Driven Enterprise
.avif)
Background
The client, a US$45 billion global biopharmaceutical enterprise founded in 1781, has presence in ~80 countries, 40 new clinical stage assets, 70 brands, over 25 manufacturing sites, and 200+ partnerships that help bring innovation to patients. The entire enterprise was run in stand-alone silos with manual processes and fragmented data. In the past few years, the organization has been on a journey to modernize its digital core but hasn’t been successful in improving the efficiencies of the business processes or gained better insights.
Improved decision-making speed
Other benefits: Risk avoidance, Reduction in defects, Improvement in business agility
Pain Point
The client's lack of digitization across enterprise processes hindered their ability to:
- Evolve into a modern, data-driven, autonomous enterprise.
- Equip Global Manufacturing, Supply Chain & Quality operations with Predictive insights.
- Monitor enterprise-wide process metrics.
- Utilize real-time connected insights.
- Foster collaboration across teams and partners.
- Achieve cost savingsDeliver faster solutions to problems.
Key Objectives of a Central Business Platform
Enhanced Visibility
Provide enterprise-wide visibility into key process and metrics
Process Digitization
Better collaboration, enhanced visibility and cost savings
Operations Optimization
Automation, operational performance, quality of service and sustainable growth
Leading Edg Capabilities
Providing more fitting, dependable, and faster solutions to new and old problems
Solution
To address the challenges, the client needed to digitize a range of processes and functions around a Central Business Platform. The processes and functions that had to be transformed included:
- The ability to view and monitor end to end manufacturing processes.
- Material Lookup (to evaluate usage of banned materials).
- Disposition of production materials/ingredients and finished products.
- Enterprise Risk Management - Identify potential risks acrossthe organization.
- Using visual aids to manage tier meetings and follow-up action.
- Platform features/capabilities (to frame applications for access control, notifications, CI/CD, etc.)
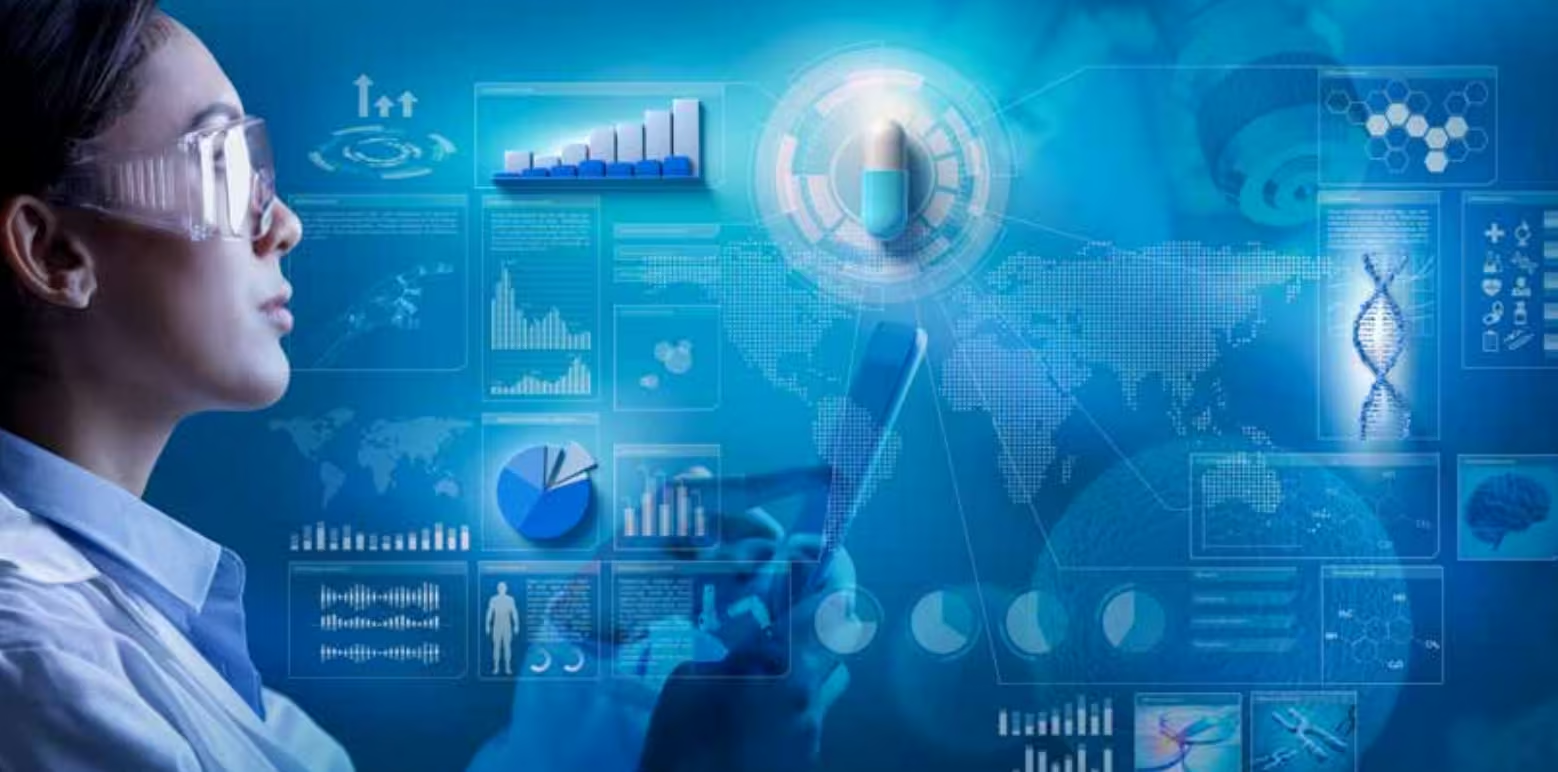
The Central Business Platform digitized and addressed these areas:
Manufacturing and Quality Control
for batch and other processes.
Supply Chain
for distribution and inventory.
Drug and Product Entities
Pharmacovigilance
for adverse event monitoring.
Reference Data
for facility, thesaurus/taxonomy, and units of measure.
In the pharma industry, effective communication between shifts on the shop floor, across functional areas, and the management is critical in maintaining product quality, reducing production errors, meeting compliance requirements, and reducing turnaround time. The existing communication model lacked standard tools. It was additionally complicated by custom solutions across groups, which did not provide a consistent view across tiers. The manual systems were also slow, operated in an unstructured hierarchy, and often resulted in inconsistent interpretation of the charts.
One of the products built under the platform umbrella, ‘Agile Operating System’ (AOS) enabled tiered communication and accountability from the shop floor to the GMSGQ leadership team using a visual system. The AOS enabled by Altimetrik provided access to real-time data aggregated across functions and shifts and displayed in a visual format, making it easier for leadership oversight and teams across five different tiers to pursue priorities and solve problems collaboratively.
The Outcomes
The Altimetrik solution connected and empowered the operations teams with data and AI-enabled digital capabilities so the enterprise could:
View, manage, and identify bottlenecks for:
- The manufacturing processes.
- The disposition processes.
- The shipping processes.
Preventing Stockouts
Visual Tools for Operational Meetings
Use visual tools to run tier meetings and follow up action across operational units and sites.
Material Usage Ban Search Functionality
Leverage a search functionality to evaluate potential usage bans of materials in pharmaceutical manufacturing.
Risk Analysis and Decision Support Dashboard
Identify, analyze, and focus on risks using adashboard to help with decision-making, reduce costs, and create more value for stakeholders.
Enhanced Adverse Event Monitoring
Improved pharmacovigilance/ adverse event monitoring.
Platform Feature Development and Scalability
Build platform features (Frame application, access control, notifications, etc.) and platform capabilities (CI/CD, Architecture, etc.).
Estimated 2,200-Hour Cost Avoidance
The AOS helped an estimated cost avoidance of up to 2,200 hours for one site.
Conclusion
The successful implementation of the Central Business Platform and the AOS ensured an end-to-end digital solution to promote cross-functional collaboration between the client’s product teams - Biologics, OESSM, and Plasma with Supply Chain, Quality, SBE, and DD&T. The client is now a modern, agile, self-driven digital enterprise.