Data Analytics Boosts Supply Chain Efficiency for Chocolatier
.avif)
Background
In January 2021, a renowned manufacturer of artisanal chocolates operating across the US, Asia & Europe, embarked on a transformative journey in collaboration with Altimetrik. The partnership commenced with a strategic road mapping exercise, aimed at delving deep into the organization’s core challenges and propelling it towards digital evolution.
Marked by dwindling margins and the pervasive impact of the COVID-19 pandemic, the client faced pressing imperatives. The need for trustworthy data permeated every aspect of their operations, compounded by the urgent call for a digital-first approach to adapt to rapidly evolving market dynamics.
Altimetrik’s engagement encompassed a holistic evaluation of the clients’ business ecosystem, from demand and supply planning to production, inventory management, finance, and sales operations. This comprehensive approach unearthed Background critical pain points, highlighting the need for digital solutions, process automation, and data analytics. The clients’ revenue model, underpinned by two distinct businesses - the traditional retail model and specialized collections, accentuated the complexity of their operations. With chocolates sourced and manufactured across multiple locations, including US & Europe, maintaining seamless operations posed a formidable challenge.
The convergence of these factors underscored the criticality of the partnership between the client and Altimetrik. It set the stage for a collaborative journey towards digitization, laying the groundwork for a compelling case study in leveraging technology to overcome operational hurdles and drive sustainable growth.
Pain Point
A journey from artisanal craftsmanship to digital agility
In the heart of Europe, a renowned chocolatier confronted the monumental task of transitioningfrom artisanal craftsmanship to factory manufacturing, grappling with the complexities ofinventory management. Challenges arose as sales plans failed to seamlessly synchronize withdemand forecasts and supply plans, exacerbated by manual adjustments due to the lack of level loading. Unclear visibility into product expiry dates left the chocolatier susceptible to disruptions, while issues with aging and best-before dating added further complexity to inventory management.
Technological barriers compounded operational challenges, with manual hand-offs acrosssales, demand, purchase, and production functions leading to inefficiencies. Amidst the globalpandemic’s turmoil, dwindling margins and a critical shortage of timely and accurate dataexacerbated the chocolatier’s woes. Once relied upon for its simplicity, Excel sheets nowhindered the flow of vital information across the organization.
With a systematic approach, Altimetrik delved into the chocolatier’s pain points, identifying three critical areas for improvement: master data, inventory reporting, and order tracking.
Collaborating closely with the chocolatier’s teams, Altimetrik embarked on a transformative journey, leveraging data analytics and process automation to streamline operations. From SKU-level supply planning to real-time visibility into product expiry, every aspect of the chocolatier’s business underwent meticulous scrutiny.
Through iterative sprints and a steadfast commitment to tangible results, Altimetrik empowered the chocolatier to embrace digital agility while preserving its rich heritage. As the partnership flourished, the chocolatier emerged stronger, poised to thrive in an ever-evolving marketplace.
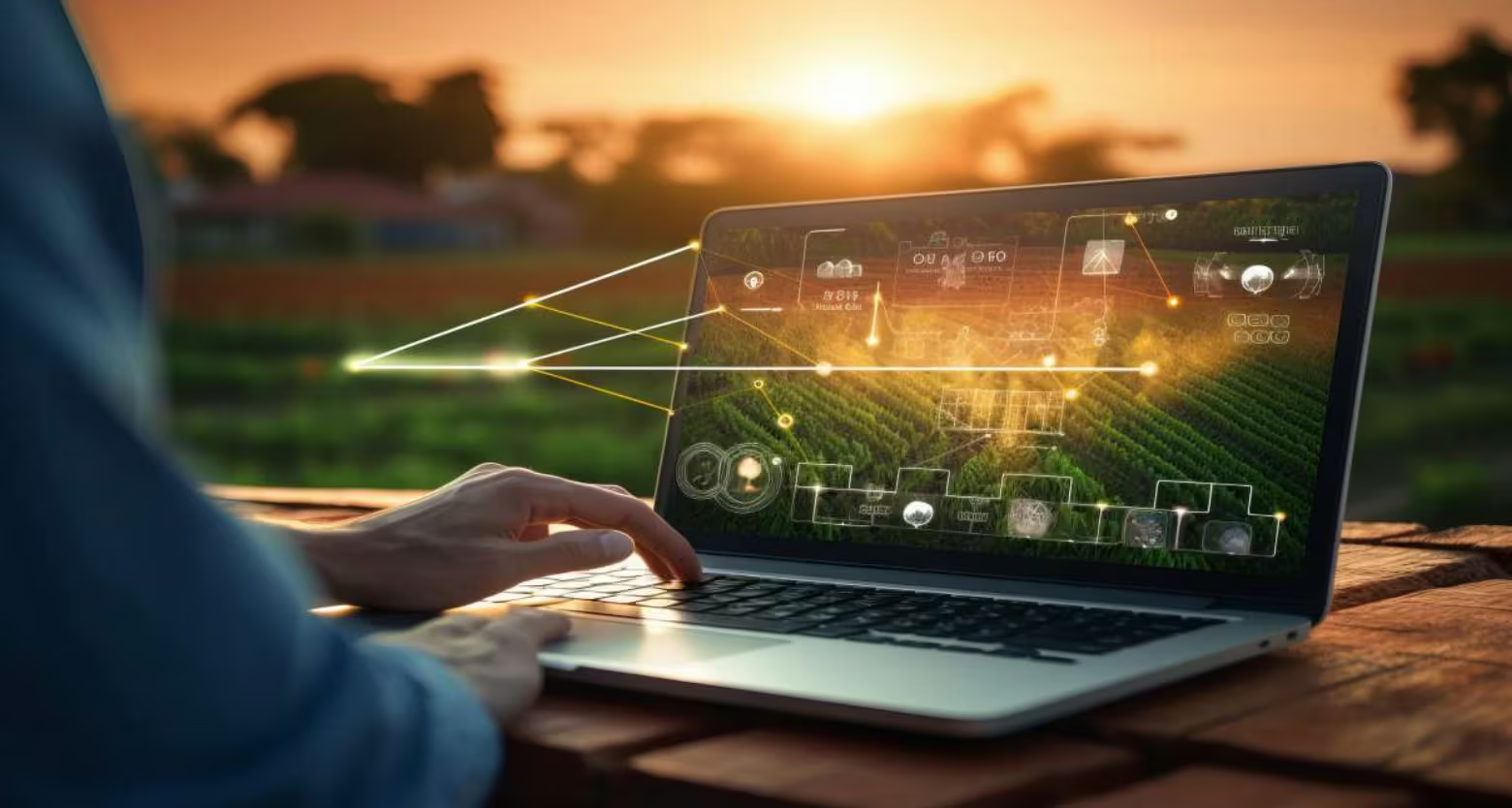
Solution
Establishing master data foundation
Altimetrik kickstarted the transformation journey by establishing a robust master data foundation. This pivotal step ensured that the European chocolatier had access to accurate and reliable Product Master, laying the groundwork for informed decision-making and a successful digital-first approach.
Building the Single Source of Truth (SSOT) platform
To address data accuracy and accessibility challenges, Altimetrik constructed a centralized SSOT platform. This platform served as a reliable repository, enabling real-time data extraction from ERP and other applications (Planning, Forecasting, Inventory management etc..). By establishing the SSOT platform, Altimetrik empowered the chocolatier with timely and accurate data insights, facilitating strategic decision-making and operational excellence which was one of the key challenges for the Chocolatier.
Real-time inventory dashboards
Altimetrik developed real-time inventory dashboards, providing stakeholders with comprehensive visibility into inventory positions and order statuses. These dashboards facilitated data-driven decision-making and improved operational agility. With access to real-time inventory insights, the European chocolatier optimized its supply chain efficiency, ensuring optimal inventory management and timely fulfilment of customer orders.
Fostering convergence among business units
Facilitating collaboration and coherence in data governance, Altimetrik fostered convergence among business units. This initiative aimed to align processes and priorities across different departments, driving organizational efficiency and effectiveness. By fostering convergence among business units, Altimetrik enabled the European chocolatier to break down organizational silos and cultivate a culture of cross-functional collaboration, ultimately driving business growth and innovation.
Streamlining operations with workflow automation
Altimetrik implemented end-to-end process automation, streamlining workflows, and reducing manual intervention. This automation enhanced operational efficiency and responsiveness, enabling the organization to adapt quickly to changing market dynamics. With automated workflows in place, real time data of orders and inventory the chocolatier optimized operational processes, achieving greater productivity and agility in responding to market demands.
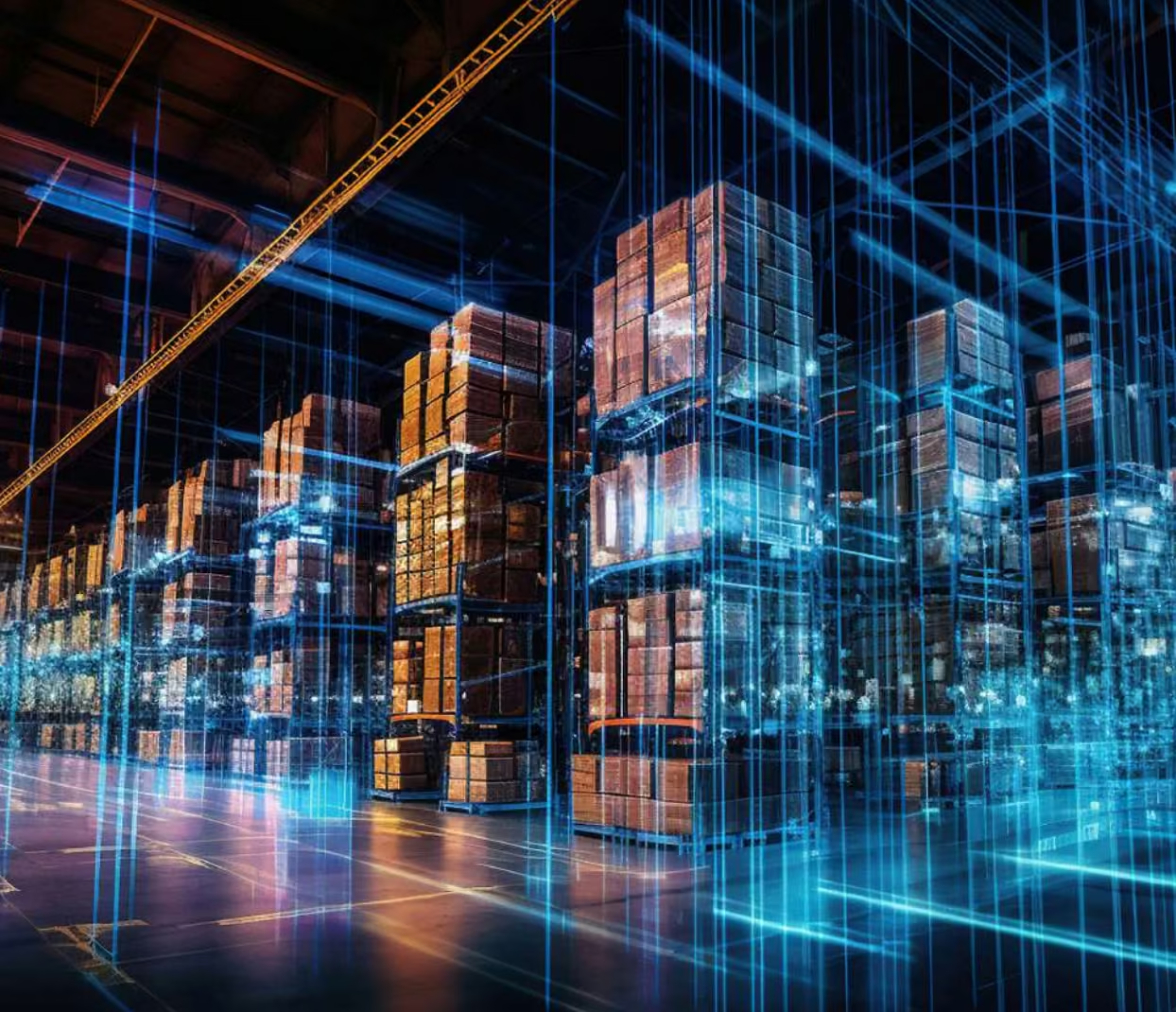
Outcome
Enhanced supply chain efficiency and inventory optimization
The implementation of data analytics-driven solutions led to a remarkable enhancement in supply chain efficiency and inventory optimization. By leveraging master data management, the client achieved the target goal of developing end-to-end real-time visibility into inventory positions, demand, and supply chain status.
This visibility empowered the organization to make informed decisions based on metrics and key performance indicators (KPIs), driving operational excellence.
20% reduction in decision cycle times
With data-driven insights at their disposal, the client experienced 20% reduction in decision cycle times. This significant reduction expedited operational processes, resulting in heightened efficiency across various business functions.
By harnessing real-time data analytics, the organization achieved agility in decision-making,enabling swift responses to market dynamics and customer demands.
Optimized logistics operations
The acceleration of re-supply notifications by 30% marked a pivotal achievement in optimizing logistics operations and inventory management. By automating the re-supply process and leveraging advanced analytics, the client streamlined logistics workflows, reducing lead-time and minimizing stockouts.
This optimization ensured seamless supply chain operations and enhanced customer satisfaction.
Improved engineering efficiency
The implementation of data-driven solutions led to a notable improvement in engineering efficiency. By automating workflows and integrating legacy systems with modern technologies, the client achieved greater efficiency in engineering processes.
This enhancement enabled the organization to allocate resources more effectively, driving innovation and accelerating product development cycles.
Comprehensive visibility with key dashboard groups
Five key dashboard groups provided the client with end-to-end visibility into inventory management and supply chain operations. These dashboards offered insightful analytics and real-time updates on inventory positions, demand forecasts, and supply chain statuses.
This comprehensive visibility empowered stakeholders to make informed decisions, optimize resource allocation, and proactively address operational challenges.
In summary, the case of the European chocolatier underscores the fusion of tradition and technology, showcasing the transformative impact of collaborative innovation. Guided by Altimetrik, the chocolatier embarked on a journey towards heightened efficiency and prosperity, seamlessly integrating time-honoured craftsmanship with advanced solutions to redefine confectionary excellence.