Top Manufacturing Trends for 2025: AI, Cloud, and Sustainability
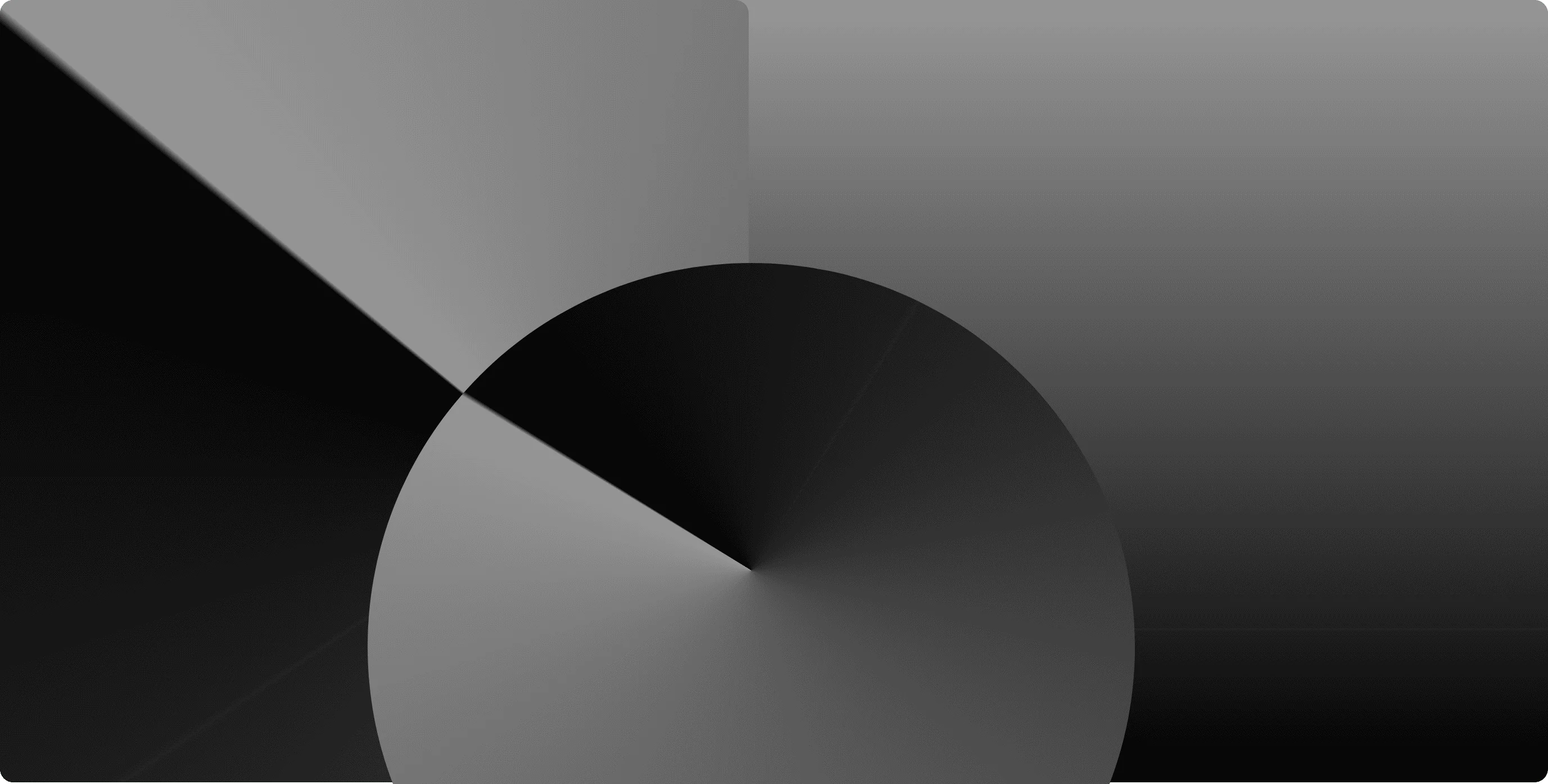
Top Manufacturing Industry Trends for 2025
The manufacturing industry has always been synonymous with innovation, adapting to the tides of technology and societal change to fuel progress. As we approach 2025, we witness that the convergence of AI, IoT, and cloud computing is driving this transformation, but it goes beyond technology. Manufacturers are reimagining processes to be more agile, efficient, and sustainable, reshaping how goods are made, delivered, and customized for global markets.
Amid supply chain disruptions and rising sustainability demands, trends like hybrid cloud adoption, closed-loop manufacturing, and AI-driven hyper-personalization are unlocking new opportunities while enhancing operational efficiency.
Hybrid Cloud
A few years back, manufacturers were reluctant to move to cloud due to OT data protection and vulnerable cloud security. But few manufacturing companies are ready to move from on-prem model to either hybrid or completely cloud to implement Industry 4.0 use cases much more in a faster way.
In 2025, companies can adopt a hybrid approach where non-critical data can be loaded onto the cloud and plant OT data can be kept on-premises. Edge analytics will be in focus as on-prem devices and servers will be hosting critical data which needs to be processed locally. Several clients are moving in this direction.
Closed Loop Manufacturing
The manufacturing floor comprises numerous systems and sub-modules, each playing a vital role and generating critical data points. To unlock the full potential of digitization, these data points must be contextualized and integrated across systems, including non-shopfloor enterprise systems within the IT layer. Achieving seamless OT-IT integration requires overlaying IT enterprise data onto the OT manufacturing layer. For instance, if SCADA or PLC systems aren’t connected to the MES layer, or if the MES layer isn’t integrated with an IoT platform, the OT layer remains incomplete.
Similarly, if PLM fails to enable dynamic BOM material allocation on the shop floor or ERP orders are not synchronized with production issues, integration gaps persist. Recognizing the limitations of siloed digitization, manufacturers are increasingly shifting towards comprehensive system integration to overcome these challenges.
AI Adoption
The adoption of GenAI models offers significant benefits for industries, particularly in enhancing customer experience and enabling hyper-personalization. These models can analyze consumer behavior patterns, detect product defects early by leveraging vast customer data, and provide immediate feedback to engineering. Manufacturers must explore how GenAI can drive personalization in their products.
The focus will be on generating complex designs, extracting insights from multimodal and large datasets, and effectively managing incomplete or ambiguous information. Tiny machine models will emerge, capable of analyzing structured data alongside sounds, vibrations, and images from machines, blending them to create innovative schemas for future applications.
Hyper-Personalization & Mass Customization
In 2025, trends will be towards creating unique experiences for every customer. With the infusion of AI technology, each customer’s individual likings and behavior will be stored. This will help industries customize their products as per customer segment. Your mobile device, car etc. will be much more personalized going forward.
This hyper-personalization will bring mass customization, and factories must be ready with multiple variants with localized 3D printed materials / objects.
Supply Chain Digitization
In many cases, the supply chain is still not an integrated part of the manufacturing. Industries can’t be behind in this integration. Robotics Process Automation (RPA) has been in the industry for a long time but still the integration of different suppliers with integrated systems is still missing in many places. The production delay is getting affected as there is no visibility & control over suppliers’ deliverables. This is also hampering the dynamics changes in the product line.
As a future trend, more work will happen towards supply chain digitalization. Legacy systems will be replaced by standard software.
Sustainability and Carbon Neutrality
Carbon neutrality has become a key focus for companies aiming to adopt sustainable practices and reduce their carbon footprint. Energy optimization, a critical Industry 4.0 use case, offers both high ROI and sustainability benefits.
The emphasis will be on reducing Scope 1, 2, and 3 emissions by implementing advanced systems and technologies across large buildings, commercial complexes, and factory floors. Additionally, employee engagement programs will play a pivotal role in fostering a cohesive approach to achieving sustainability goals.
IOTization
Many organizations started with digitization as they don’t want to be left behind the hype which was created a few years back. They started with small PoCs or projects, implemented basic IOT modules and expected large benefits to flow in as the industry was projecting. They connected their sensors and machines and started collecting their real time status through some of the basic IOT modules. This is fine but you will neither get larger benefits of digitization with such basic steps nor can you call the IOT platform robust and scalable.
Virtual Factories
With 5G and satellite internet broadband speed and uninterrupted availability, many Industry 4.0 use cases which were earlier having challenges will be possible now. With the advent of digital twins, AR / VR advancement, more replicas of the entire factory system will be created.
Virtual factories will bring new standards of remote diagnostics which in turn will bring efficiency.
Digital Thread
In 2025, the challenges of limited digitization benefits caused by siloed approaches will be addressed with greater adoption of digital thread implementations. System engineering, a crucial stage in product design, will see enhanced integration of tools like CAD, CAM, and PLM systems with MES and ERP systems. Virtual factories will set new benchmarks in remote diagnostics and driving efficiency.
As mass customization and personalization shape the industry, the effective implementation of the digital thread will become pivotal to success.
The manufacturing sector has always led the charge in embracing innovation, integrating robotics, the internet, and material science advancements seamlessly. In 2025, it faces a dual challenge: harnessing artificial intelligence amid rapid technological disruption and addressing urgent sustainability demands as the climate crisis escalates. Adding to this is the need to build resilience against geopolitical and societal uncertainties.
To stay competitive, manufacturers are doubling down on breakthrough technologies while reshaping workforce strategies, rethinking skills, and investing in future-ready training. The sector’s ability to adapt will define its role in shaping a sustainable, resilient, and innovation-driven future.