Manufacturing Digitization Challenges: Overcoming Barriers to Unlock Potential
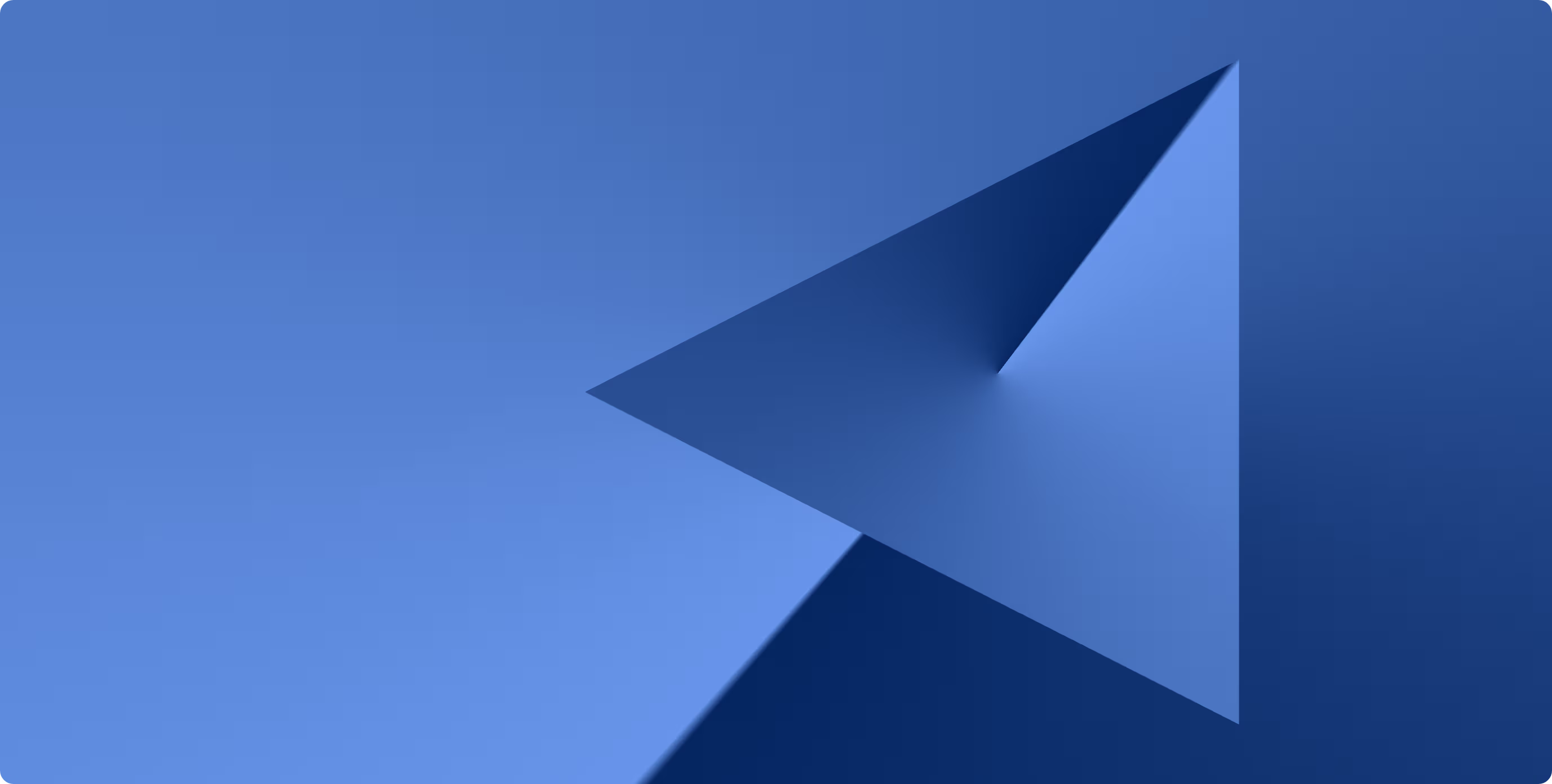
The manufacturing industry is undergoing a profound transformation driven by the rapid advancement of digital technologies. From IoT and AI to cloud computing and automation, the opportunities for efficiency, innovation, and growth are unprecedented. However, while the promise of digitization is vast, the journey toward achieving it is not without obstacles. Many manufacturers face hurdles such as limited IoT implementations, fragmented systems, and resistance to change, which impede their ability to fully realize the benefits of intelligent manufacturing. Understanding and addressing these challenges is key to not just staying competitive but thriving in the era of Industry 4.0.
The Struggle of Half IoTization
Many organizations began their digitization journey by implementing small-scale proof-of-concept (PoC) projects or basic IoT modules. These initial efforts, often driven by the hype surrounding IoT, were aimed at connecting sensors and machines to collect real-time data. While these steps marked a promising start, they were limited in scope, often lacking the scalability and robustness required to achieve meaningful transformation. Without enterprise-wide integration and advanced analytics, such efforts cannot deliver the substantial benefits of digitization. To overcome this, manufacturers must shift their focus to scalable IoT platforms capable of handling high data volumes and delivering actionable insights. Moving beyond isolated implementations to a holistic strategy is essential for maximizing the potential of IoT in manufacturing.
Incomplete Integration: Bridging IT and OT Systems
On the manufacturing shop floor, numerous systems such as SCADA, PLC, MES, and ERP collect critical data, each playing a vital role in operations. However, these systems often operate in silos, leading to incomplete integration and underutilized data. For instance, if SCADA or PLC systems are not connected to the MES layer, real-time production insights are inaccessible. Similarly, without integration between PLM systems and ERP systems, the operational loop remains incomplete, resulting in inefficiencies and missed opportunities. To address this challenge, manufacturers must prioritize seamless IT-OT integration. This involves contextualizing data across systems to create a unified operational view, enabling better decision-making and greater agility.
The Mindset Barrier: Overcoming Resistance to Change
Cultural resistance remains one of the most significant barriers to manufacturing digitization. The industry has historically been slow to adopt new technologies, often adhering to the principle of “don’t touch unless it’s broken.” This cautious mindset, coupled with concerns about disrupting daily production targets, hinders progress. Shop floor operators and production managers may resist updating workflows or systems due to fear of short-term inefficiencies. Overcoming this resistance requires strong leadership and a culture of innovation. Change management programs, clear communication of benefits, and showcasing success stories can help drive the necessary shift in mindset. Leaders must emphasize that embracing digitization is not just about staying competitive but about ensuring long-term survival.
Conclusion: A Roadmap to Success
Manufacturing digitization offers immense potential for innovation, efficiency, and resilience. However, the journey is not without its challenges. Overcoming barriers such as Half IoTization, incomplete system integration, and cultural resistance demands a comprehensive approach that combines scalable technology investments, seamless integration, and a forward-thinking mindset. By addressing these challenges, manufacturers can unlock the full benefits of digitization, paving the way for sustained growth and success in a rapidly evolving industry. The time to act is now—embrace digitization not just to remain relevant but to lead in the future of manufacturing.